SHINKOH METAL's
5 strengths
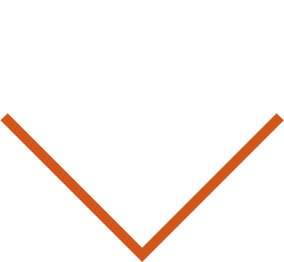
Trial production systems capable of meeting extremely tight deadlines
Our self-hardening line has a proven track record of experience and results in production of a wide variety of quick turnaround, high difficulty cast components, particularly in trial manufacturing of aluminum castings for automotive parts. In addition to producing molds at our in-house factorys, we also increasingly handle direct fabrication of sand molds (casting molds) from 3D CAD data, allowing for even faster turnaround times.
> See details
Approximately delivery times for prototypes via 3D laminate sand mold casting
3D printer production of sand molds (casting molds) |
We can produce cast products in as little as 10 days if 3D CAD data is available. This is the optimum method for cases where procurement deadline is the priority, or when producing only 1 cast product with no die. |
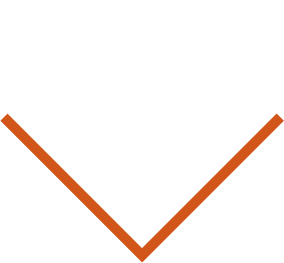
Optimal casting plan design using simulation technologies
Controlling blowholes which occur inside castings is a major issue for the casting process. The introduction of casting fluidity simulations allows for the prediction of where blowholes will occur (defect occurrence locations), which makes it possible to design optimal casting plans.
> See details
Fluidity simulation
Setting simulation
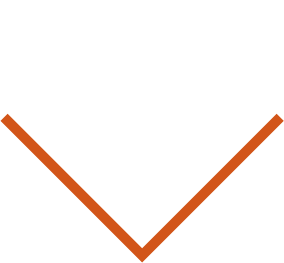
Inspection and quality assurance systems backed by abundant experience in the trial production business
In order to establish a satisfactory quality assurance system, we employ not only inspection equipment within our plants, but also utilize inspection equipment at group companies and affiliate companies based on customer requirements.
> See details

Cast-in joining technologies for ferrous and aluminum metals
One of our major strengths is that we have our own cast iron and aluminum casting plant which is also capable of "cast-in" technologies where ferrous metals (cast iron, stainless steel, etc.) are cast inside of aluminum castings. As industrial machine parts have continued to become more compact and more advanced in recent years, there has also been an increase in cast-in technology needs.
> See details
-
Technology overview
Aluminum/ferrous metal mixed castings require review of design and forms for cast-in part core prints. In addition, as there will be no adhesion between the differing materials, it is also important to maintain control in order to prevent any gaps from occurring.
-
Value provided by technology
Casting-in of pipes provides the component with its own cooling feature, which both improves cooling performance and also saves space.
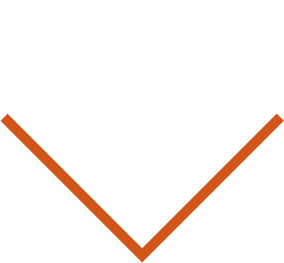
Ultra-thin-wall casting via HVC
echnologies (vacuum degassing)
Vacuum degassing (HVC) of cast iron improves molten viscosity and allows for production of ultra-thin-wall castings, while also reducing shrinkage cavities and improving yield rates.
> See details
What is HVC (Higher Valuable Casting)?
■Our company's original casting technology which makes it possible to achieve higher quality molten metal through molten metal processing (vacuum degassing).
■Compared to standard molten metal, molten metal processed via this method can be expected to have improved fluidity, thinner walls and lighter weight, improved machinability, decreased level of defects, and higher yield rates.
Pushing the limits of thin-walled casting using our original casting technologies
1Thinner walls and lighter weight |
» |
The limit of wall thickness for conventional castings is generally considered to be approximately 4-5 mm, however by controlling the gases in molten metal, we are able to produce ultra-thin-walled castings (no-chill casting) of 1-2 mm. |
2Machinability improvement |
» |
HVC processed materials increase ferritic matrix by 20-30% over normal cast iron which greatly improves machinability. |
3Reduced level of defects |
» |
Promotion of ferritization can reduce shrinkage cavities, which are internal defects, which in turn reduces the level of defects. |
4Improved yield rate |
» |
HVC processing allows for reduction of dead head (feeder) which can result in an improved planned yield rate of 10% or more. |